SAFETY FEATURES
- While operating a rapid mixer granulator it is important to check and confirm the locking mechanisms.
- While operating a rapid mixer granulator it is important to check external resources for controlling and monitoring various parameters.
- While operating a rapid mixer granulator it is important to check the availability of external emergency shutdown switches.
- While operating a rapid mixer granulator it is important to check the availability of fire protection resources means for electrical systems and drives that are used.
CONTROL SYSTEMS
- Manual Control – Process Timer for Main Motor & Chopper.
- AMP Meter for Main Motor of chopper.
- On/Off Push Button.
- Auto Control – PLC based with touch Screen and password level to feed the parameter of process for Wet / Dry Granulation.
- Pre-stored process parameter will help to achieve consistent product quality.
- MMI (Touch Screen) for visualization of machine of specific process condition and data.
- PLC indicates: Visualization of Machine process condition & date.
- Alarm Signal & Fault Message.
- SCADA package (OPTIONAL)
OPTIONAL FACILITY AVAILABLE ON DEMAND AT EXTRA COST
WHAT IS GRANULATION?
- Granulation involves the process of gathering particles together through the creation of bonds between them.
- In generating bonds during the granulating process, binding agents or compression are used.
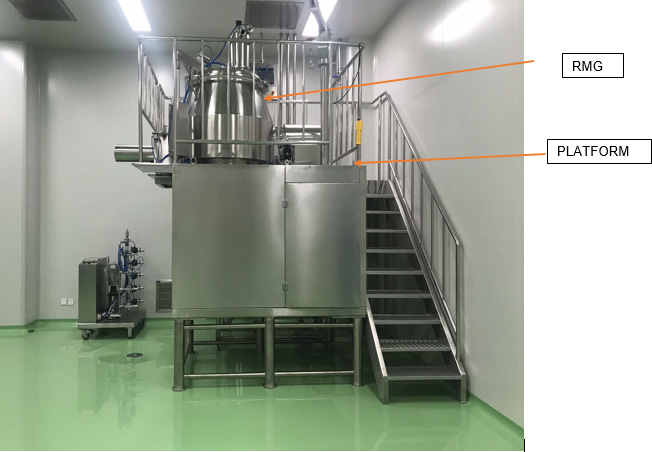
- High Shear Mixer Granulator, Inline Mixer, Rotor/Stator Mixer
- What does a Rapid Mixer Granulator (RMG) or High Shear Mixer Granulator do?
- Parts of a Rapid Mixer Granulator (RMG) or High Shear Mixer Granulator and their functions
- SMP Shear Mixer mainly contains a loading system, impeller system, spray system, chopper system, CONE MILL (as an optional item) system, control system, etc.
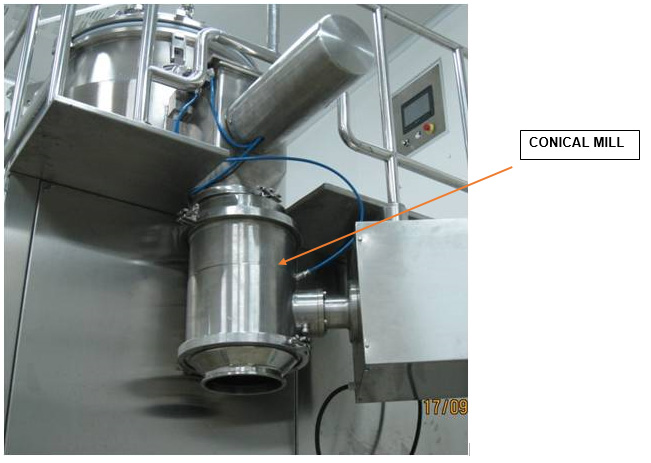
- Conical Mill + High Shear Mixer Granulator.
- A rotor or vein along with the stationary mechanical device. Also, the fixed part can be an associate array of stators and rotors. The device is engaged with a tank containing the ingredients to be mixed.
- A pipe is passed for the passage of the ingredients to form a Shear.
- The Rapid Mixer Granulator (RMG) or High Shear Mixer Granulator produces granular products that can be used in a pharmaceutical company.
- Other types of the high Shear mixer can generate suspensions (gas distributed in liquid) as well as emulsions.
- The result of the granulation process can also be employed in other industries besides pharmaceuticals.
- SMP Rapid Mixer Granulator (RMG) or High Shear Mixer Granulator also widely used in health products, food, cosmetics, chemical, the cosmetics industry, and adhesives derived from homogenization, emulsification, particle size reduction, and dispersions.
- In the high Shear mixer granulation process, the solid part of the mixture is required. Fluids or solutions are used to serve as an associate that aids the process.
- After the solid part has been formed, it is chopped down to the needed particle size which is subsequently passed to the drying bed.
- From the drying bed, the fluid is completely removed to form granulated products.
- Features of mixing machine or Rapid Mixer Granulator (RMG) or High Shear Mixer Granulator
- The equipment is beautifully designed to appeal to the eye. There are various product types and designs from different manufacturers of Rapid Mixer Granulator (RMG) or the High Shear Mixer Granulator.
- However, all the designs on SMP follow Current Good Manufacturing Practices compliance (cGMP) and the US FDA.
- Also, our Rapid Mixer Granulator (RMG) or High Shear Mixer Granulator carries out the automated mixing and granulating process using a single bowl.
OPERATATION SYSTEM
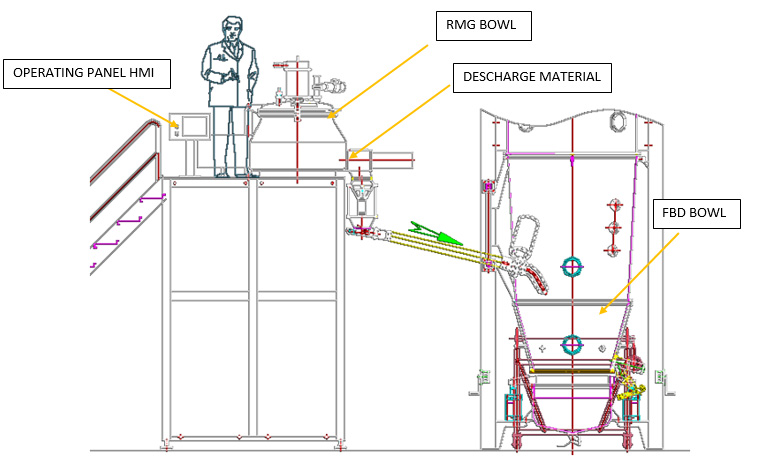
- Vacuum conveying + High Shear Mixer Granulator You can add binder by spraying the system with a peristaltic pump, pneumatic diaphragm pump, and pressure tank, it is according to your process and capacity requirements, gear while there is the flameproof electric motor in place.
RAPID MIXER GRANULATOR (RMG) OR HIGH SHEAR MIXER GRANULATOR SAFETY FEATURES.
WITH HIGH SMP SHEAR MIXER GRANULATOR, YOU CAN BE SURE OF OPTIMUM SAFETY WITH THE ADEQUATE FEATURES IN PLACE.
- Open bowl cover state, impeller and chopper can’t work, there is logical protection.
- It has an enclosed total drive transmission system with a limit switch top lid installed to guide against the accidental opening of caps during operation.
- Automatic Also, the pressure switch is installed so that you can ensure optimum pressure in the equipment.
- There is an emergency stop button and overload relay protection to prevent accidents during use.
- Also, an explosion-proof system (AS AN OPTIONAL ITEM) is available on your request.
- The explosion-proof design includes an explosion-proof touch screen, explosion-proof junction box, explosion-proof winding tube, explosion-proof motor.
- Production Rapid Mixer Granulator (RMG) or High Shear Mixer Granulator parts:
- WIPs system is an (OPTIONAL ITEM) of Rapid Mixer Granulator (RMG) or High Shear Mixer Granulator; it can share one set of WIP system with fluid bed equipment.

- WIP SYSTEM + HIGH SHEAR MIXER GRANULATOR
CHAPTER 2: The Dosing System Types
- Ensure to check the dosing system type that is in place in your granulator machine.
- Is it a manual or automatic system?
- Does it include a binding solution or powder dosing system?
- Whichever works for you is what you should go for.
- Nevertheless, you have to put in mind the purpose of purchasing the mixer machine in the first place.
THE IMPELLER BLADE DESIGN
- The granulation process efficiency is determined by the design that the impeller blade carries.
- A typical homogenizer mixer primarily has different numbers of blades which can be up to three in some granulator machines.
- Another factor you need to put into mind is the design and the position of the impeller blade as they are of equally great significance.
- High Shear Mixer Impeller & Chopper – Rapid Mixer Granulator
- Usually, in Rapid Mixer Granulator (RMG) or High Shear Mixer Granulator, the position of the impeller tip is lateral to facilitate to reduce the probability of dead spots.
- The function of the impeller is to mix and form granules.
- Also, the rotation speed of the homogenized mixer depends on the specification of the machine including the design.
- Position of the impeller Rapid Mixer Granulator (RMG) or High Shear Mixer Granulator s are classified based on usage; there is a laboratory-style of the high shear mixer and the production style.
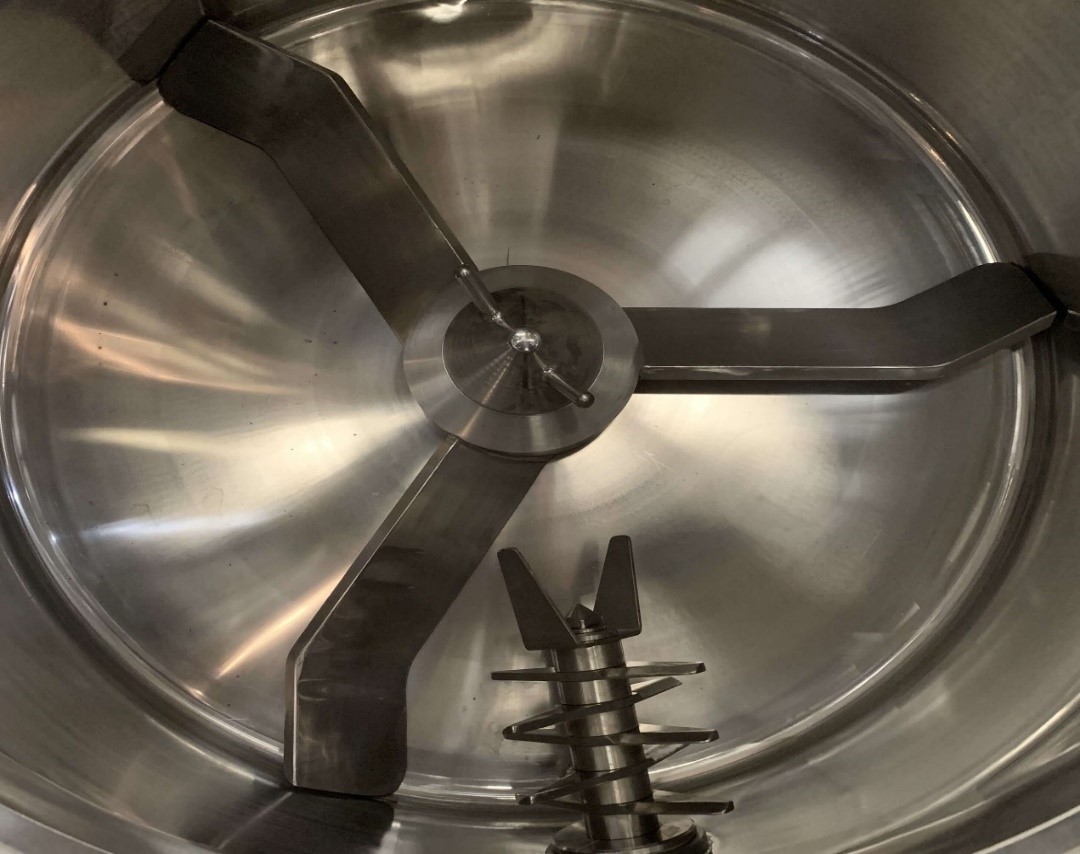
CHAPTER 3: How Rapid Mixer Granulator (RMG) Or High Shear Mixer Granulator Works
- Are you interested in how high shear mixer works?
- The technology behind the high shear mixer is complex and fascinating.
- Regardless of the brand, you are choosing, high shear homogenizers follow similar approach om carrying out their granulation operation.
- The working principle of Rapid Mixer Granulator (RMG) or High Shear Mixer Granulator follow the following processes;
- Mixing of the powder
- The high shear granulation process starts with the mixing of the powder in a bowl using the impeller.
- Addition of binder or granulation liquid
- Next, the impeller proceeds to mix and spread the granulation liquid also known as a binder at a speed between 5rpm – 300rpm (As per depend Powder)
- Dampening or wetting of the powder
- The Rapid Mixer Granulator (RMG) or High Shear Mixer Granulator ’s part, the chopper breaks the wet lump to generate granules at a speed of 200 -1440rpm.
- Nucleation process (formation of crystals powder)
- At this stage, you will notice the formation of crystal powder otherwise called the nucleation process.
- Granule growth and densification of powder.
- Agglomeration of granule or the power densification occurs next through the incorporation of granulation fluid into the powder using high-power-per-unit mass. This process is achieved through the rotation of the high shear forces.
- Breakage and attrition of granule.
- The granulation process ends with the breakage and attrition of granules which is then transferred to wherever it is needed whether for pharmaceutical purposes or other industrial uses.
CHAPTER 4: High Shear Mixer Wet Granulation Process Guide
- We will be looking at the wet granulation process.
- You can rest assured that this chapter will answer all the questions you have concerning the wet granulation process of the high shear mixer.
- We will be checking some of the questions you may have such as: What are the problems you can encounter while using Rapid Mixer Granulator (RMG) or the High Shear Mixer Granulator?
- How can you balance a successful test on a laboratory high shear granulator and a production failure in high shear granulation machine?
- What are the difficulties that you can encounter during lab wet granulation process amplification?
- This chapter covers areas such as the wet granulation equipment, and how you can master the wet granulation process as a user or an operator of pharmaceutical equipment.
- Several factors can affect the wet granulation process particularly connectivity during amplification.
- What you should know about the wet granulation process.
- Firstly, it is important to note that the wet granulation process mostly occurs in solid dosage forms.
SMP, the leading supplier of the high shear mixer in China ensures the scalability from R&D high shear mixer supplying to putting level Rapid Mixer Granulator (RMG) or High Shear Mixer Granulator for sale.
TECHNICAL SPECIFICATION OF RAPID MIXER GRANULATOR
GROSS CAP LITERS |
WORK CAP LITERS |
WORK CAP KG |
MAIN MOTOR 750 / 1500 |
GEAR BOX |
CHOPPER MOTOR 1500 / 2880 |
DISCHARGE HT |
SPACE REQUIRED L X B X H MM |
25 |
20 |
5 - 10 |
3 / 5 |
4' |
1.5 / 2 |
600 |
650 X 1200 X 1100 (1250) |
100 |
80 |
10 – 30 |
7.5 / 15 |
5” |
2 / 3 |
780 |
1500 X 2200 X 1800 (2175) |
150 |
120 |
30 – 60 |
7.5 / 15 |
5” |
3 / 5 |
780 |
1800 X 2500 X 1875 (2300) |
250 |
200 |
50 – 120 |
25 / 30 |
7” |
3 / 5 |
1055 |
2000 X 2800 X 1920 (2450) |
400 |
320 |
100 – 150 |
30 / 40 |
8' |
5 / 7.5 |
1200 |
2500 X 3000 X 2300 (3000) |
600 |
480 |
100 – 250 |
40 / 50 |
10' |
5 / 7.5 |
1200 |
2700 X 3200 X 2300 (3000) |
1000 |
600 |
200 - 350 |
63 / 85 |
12' |
10 / 15 |
1200 |
2900 X 2900 X 2500 (3200) |
- The rapid granulator mixer whole set consists of a loading system, impeller system, spray system, chopper system, wet cone mill system (as an optional item), control system, etc.
HIGH SHEAR MIXER GRANULATOR
- SMP high shear mixers’ chopper ensures an optimum granular structure, the GM series Rapid Mixer Granulator (RMG), or the High Shear Mixer Granulator equipped with a chopper and high straight shear mixing blades.
- The position of the chopper in the lower third of the working vessel results in its very high level of efficiency, even where there are minimum filling volumes.
- SMP shear mixer granulator rapid mixer’s chopper exists in two speed or variable speed.
- Main shaft and chopper shaft are designed with one-way flow air seal, flow rate, the pressure of air seal can be measured & controlled to prevent and detect powder or water from entering inside.
- SMP super mixer auto controls stop position of the impeller; auto elevates the main shaft pneumatically for the visible check without dismantling.
- The all-important tool in the wet granulation is the bottom driven Z-Rotor.
- The unique geometry of the Z-Rotor ensures maximum efficiency while minimizing the power required.
- Cutting-edge measuring and manufacturing processes ensure that the gap between the rotor and the bottom of the working bowl is kept to a minimum while maximizing product yield.
- SMP Unique technology guarantees ease of handling.
NOTE: - We can customize all your equipment based on your requirements. Once you approve the detailed user requirement statement (URS), we can supply the Rapid Mixer Granulator (RMG) or High Shear Mixer Granulator drawing and suggestion for your factory layout.
- Also, we provide our technical support, custom design for your process and layout.
- Whether it is from laboratory Rapid Mixer Granulator (RMG) or High Shear Mixer Granulator equipment or amplifying batch high shear mixer equipment, it is generally known that it is difficult to design and amplify.
- This is because are many process parameters and competing mechanisms in the wet granulator.
- Also, the production batch Rapid Mixer Granulator (RMG) or High Shear Mixer Granulator equipment and existing production high shear mixer equipment to larger production Rapid Mixer Granulator (RMG) or High Shear Mixer Granulator equipment design is demanding too.
- In high shear wet granulation, the mother nucleus is formed at the stage where the liquid is in contact with the powder bed and the internal reaction of the powder particles.
- The growth of the mother nucleus is due to the adhesion of the powder particles to the surface of the mother nucleus or the combination of two or more particles. This step usually also makes the particles denser.
- When the force in the granulating bowl (shear force, the force from the impeller, chopper, or granulation wall) exceeds the particle strength, the particles are broken.
- Changing the above parameters may change the yield and properties of the particles. Some suggestions and comments on how to control granulation parameters will be given below.
HOW TO CONTROL GRANULATION PARAMETERS?
- Granulator geometry
- Many companies do not control the geometry of the high shear mixer, but the laboratory Rapid Mixer Granulator (RMG) or High Shear Mixer Granulator equipment is preferably selected or designed to be similar to the device with the same geometry, i.e., the same aspect ratio.
- Amplification between devices with similar geometric structures is equivalent to amplifying only the stirring impeller speed, which is much simpler. It is also essential to amplify the speed of the impeller.
- The effect of the stirring impeller rotation speed on the particle size is primarily related to the composition characteristics of the formulation and the granulation mechanism of the process.
- In some cases, increasing the speed of the impeller can increase the particle size. In some cases, increasing the speed of the impeller increases the breakage rate of the particles, resulting in a decrease in particles.
- The most important thing is to consider the air intake assembly of the high shear mixer.
- High Shear Mixer Granulator
- During the operation of many granulators, the internal particles appear twisted rope, and the powder bed moves in a circular shape in the granulating pot under the action of the air system.
- If the stirring impeller rotation speed is too low, the inside of the granulating bowl will be in a bumping state, so that the surface movement of the powder bed layer is relatively slow, and only the bumping state caused by the stirring impeller rotation speed is obtained.
- The twisted rope state is vital for the mixing of the powder in the granulating pot and the distribution of the liquid, and mainly affects the size of the mother nucleus. There have been some laws for the amplification of the stirring impeller speed. Some people advocate a constant linear velocity.
- Some people suggest that the Froude number (the ratio of centrifugal force to gravity inside the high shear mixer) is constant. Others have suggested using a continuous shear force inside the granulator, and they recommend using the following formula when zooming in NDn Where N is the angular velocity of the impeller, D is the diameter of the paddle, and n is a constant (n is found to be equal to 0.85, although this value is likely to be prescription-system dependent)
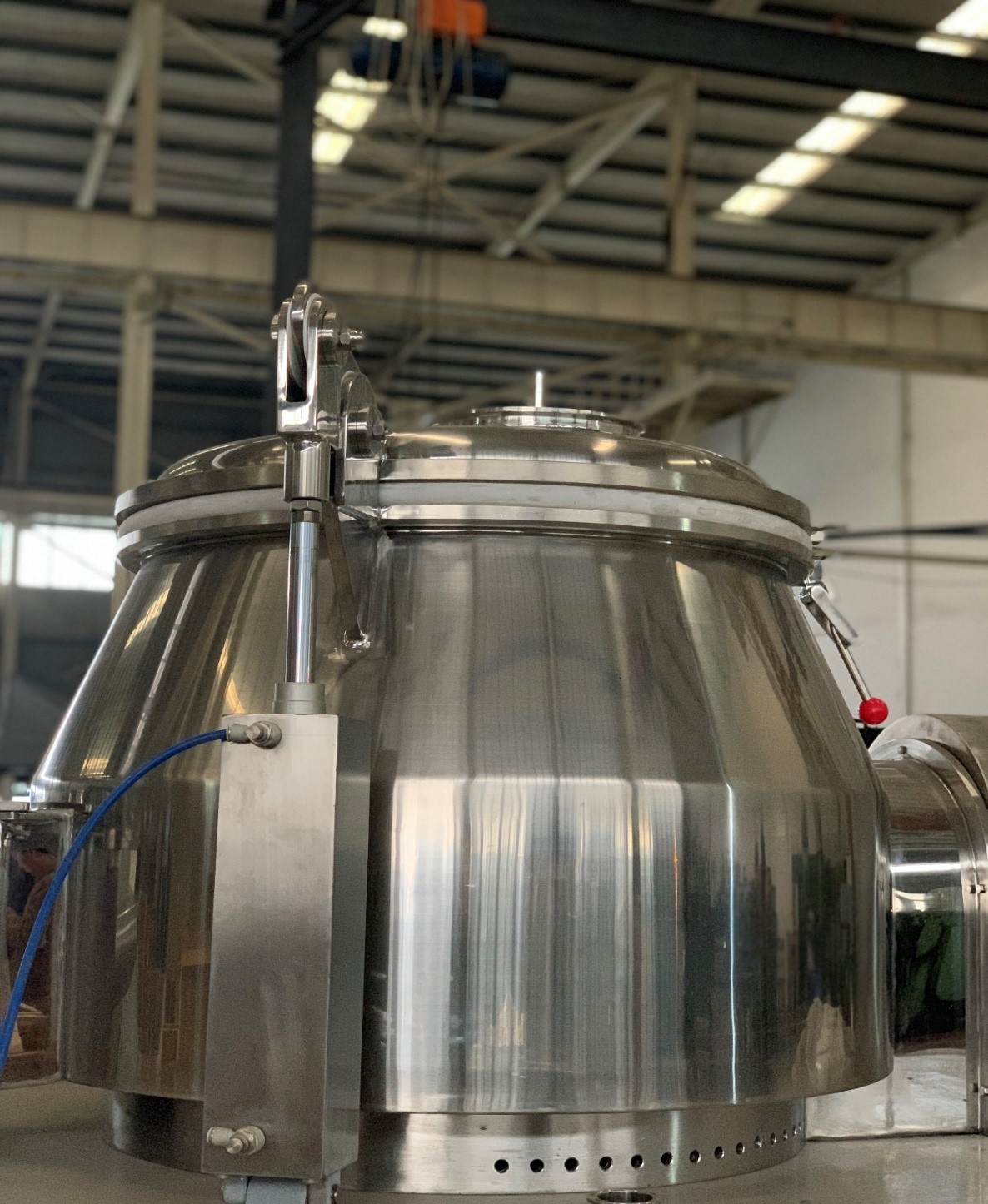
CHOPPER SPEED
- The role of the Rapid Mixer Granulator (RMG) or the High Shear Mixer Granulator chopper is not very clear. Based on the nature of most of the mixtures, we found that it neither promotes the growth of the mass, increases the compactness of the mass, or breaks the particles.
- Increasing the size of the shear mixer granulator can reduce the frequency of interaction between the granules and the chopper. In this case, it is an excellent idea to fix the linear speed of the cutting blade during the enlargement process because the particles are similarly impacted.
- However, if other variables in the amplification process cause the particles to increase, increasing the chopper speed can reduce the size of the particles.
- How to add the binder and the flow rate Some advanced particle research has been devoted to the development of a mother core state diagram that describes the nucleation process under a given granulation process.
- This map has two dimensionless parameters: the time the droplet enters the powder bed and the jet flow rate (which can be considered as the ratio of the liquid spray rate to the tumbling speed of the bed surface particles).
- The droplets enter the powder bed for a short period (i.e., droplets that quickly enter the powder bed) and low jet flow (i.e., the droplets can be sprayed well onto the powder surface), and their nucleation behaviour is controlled by droplets. That is to say, many mother cores are formed by a single droplet, and the size range of the mother core is relatively narrow.
- Either the time of droplets entering the bed increases or the increase of the spray flow rate leads to over-wetting.
- The liquid deposits on the surface of the powder bed to form a large mother nucleus. In this case, mechanical force is required to destroy it.
- Force destruction leads to a wide distribution of the size of the mother nucleus.
- The size distribution of the nucleus is the beginning of granulation.
- For many prescriptions, it is critical to forming a similar size nucleus through the granulator. If the amplification process is to achieve the state in which the mother core is controlled by the droplets, it is required that the droplet size during the amplification process is the same as the droplet size during the small test (the time when the droplet enters the powder bed is similar).
- Also, the low discharge flow rate is necessary (formation of a single sheet) for the droplet mother core to be effective. The method of reducing the spray flow rate is to ensure that the spray width covers the effective surface of the bed (i.e., the radius of the granulator).
- This is to reduce the volume flow rate of the adhesive and increase the tumbling speed of the powder during the process of wet granulation in a high shear mixer.
GRANULATION TIME:
- It is difficult to determine the effect of the granulation time on the properties of the granules by different granulators. The mechanical distribution of the liquid binder in a sizeable granulating pot requires an enormous time. However, this is primarily related to the formulation and process parameters.
- Anyway, there are so many factors control parameters, beyond what we have written above.
- That is why you should review the technology behind D&R high shear mixer and manufacturing high shear mixer to know more about the high shear mixer.
- Through theory and technical parameter specifications, I believe you have learned a lot about the high shear mixer, especially the reason for the difficulty in R&D high shear mixer to amplifying batch Rapid Mixer Granulator (RMG) or High Shear Mixer Granulator.
- SMP focus on research about technology, special combines machinery, and process which are key components from importation to production.
- Thus, SMP as a global high shear mixer rapid granulator mixer manufacturer and supplier is well versed in the sales and supply of Rapid Mixer Granulator (RMG) or High Shear Mixer Granulator.
- At SMP, we are committed to providing you quality products as we are concerned about building our brand.
- As such, we appreciate the feedback from you, not only in the aspect of reviews on machinery you purchase from us alone but also in our entire work process. They help us improve in all phases of our operation; from customer service to aftersales maintenance.
CHAPTER 5:
- Factors affecting the granulation process and Advantages of Rapid Mixer Granulator (RMG) or High Shear Mixer Granulator
- Many factors can affect the granulation process of a high shear mixer. If you are not quite familiar with how this homogenizer mixer works, you can find it difficult to know how to best make use of it.
- We have highlighted some of the factors you have to pay attention to if you want to maximize the productivity of your high mixer machine. They include;
FORMULATION VARIABLES
- The type and number of binders used as an inactive material during the granulation process will go a long way in affecting the entire granulation process.
- Physical Properties of Ingredients
- The physical properties of the materials to be granulated can play a huge role in affecting the granulation process. Physical properties such as size, hardness, and the nature of the materials should be considered.
BINDER MATERIALS
- There are several binder materials and solutions that you can use. Some of the popular excipients or binder materials used for Rapid Mixer Granulator (RMG) or High Shear Mixer Granulator include starch paste, hydroxypropyl cellulose, hydroxypropyl methylcellulose, polypropylene pyrrolidone, etc.
- Natural Binders: cellulose, acacia, gelatine, starch paste, alginic acid, tragacanthin, and pregelatinized starch
PROCESS VARIABLES
- These include all the variables that can affect the outcome of the granulation process. Listed below are some of these process variables;
- Chopper speed
- Designs of Granulator
- Methods of adding a granulating solution
- Rate of granulating solution
- Speed of Impeller
- Granulator bowl load
PLC CONTROL – The whole process control by Programmable Logic Controller. The control system is a Delta / Schindler / Innovance series stored program control (PLC). It features an operator panel unit of 4” / 7” inch Delta / Schindler / Innovance HMI panel available on your request (as an optional item). (OPTIONAL)
OUTPUT SAFETY
- Most mixing equipment will be used in the manufacturing of food and drug. As such, a very high level of safety is required.
- You should steer clear of any products that can tarnish your business image and brand reputation.
- Here are some of the factors you should look out for in your choice of Rapid Mixer Granulator (RMG) or High Shear Mixer Granulator;
EFFECTIVE WIP SYSTEM (AS AN OPTIONAL ITEM)
- Proven and trackable record on safety
- FDA and EFSA certified as equipment for food-related materials
- Compliance from components supplier regular audit
- Hygienically designed mixer and possibly EHEDG approved
- Select the most cost-effective
SEAMLESS DOCUMENTATION PROCESS
- Having to undergo a rigorous process can be tasking and frustrating. As such, SMP ensures that all documents related to the equipment guarantee easier training, operation, and maintenance of the equipment throughout our equipment’s life term for an exigent industry like the pharmaceutical market.
- We offer a complete set of cGMP documents including Qualifications (DQ, IQ, OQ, ), FAT, SAT, USER manual documentation. We perform the qualification executions as customer request.
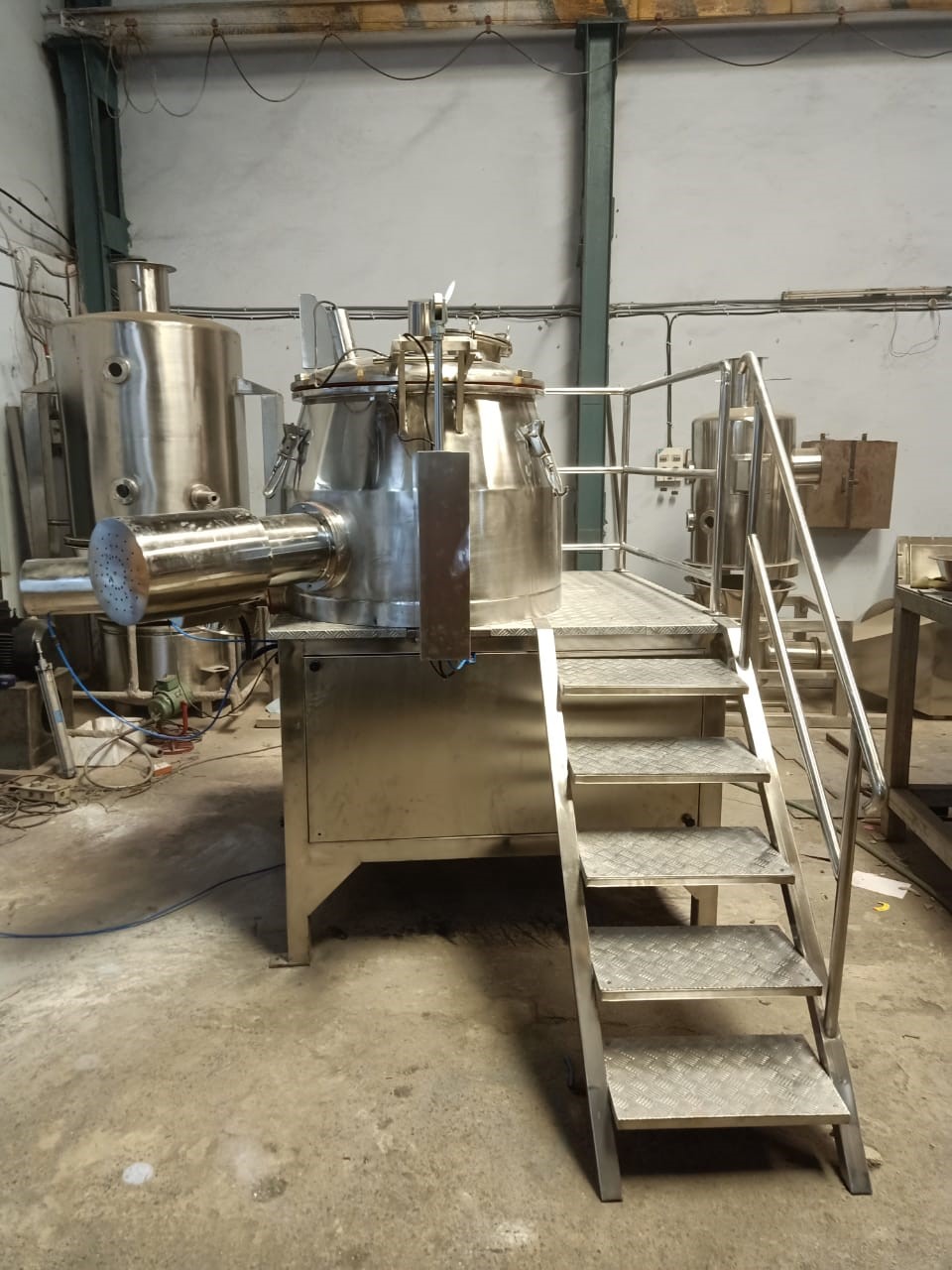